Symmetrical Group
Policies and Procedures
OHS&E\SAFETY PROCEDURES
SG-PR-33-00 Safety rules and responsibilities
TABLE OF CONTENTS
1. GENERAL DUTY OF CARE
1.1 Introduction
1.2 Employers’ Duty of Care
1.3 Employees’ Duty of Care
1.4 Compliance
1.5 resolution Of Safety & Health Issues
2. ON SITE EMERGENCY ARRANGEMENTS
2.1 Reporting A Serious Injury Or An Emergency Situation
2.2 Emergency Alarm
2.3 Muster/Assembly Areas
3. ACCIDENT, INCIDENTS & HAZARDOUS CONDITIONS
3.1 Reporting & Investigating
4. GENERAL SAFETY RULES
4.1 General Safety Rules
4.2 Vehicles And Mobile Equipment
4.2.1 Drivers and Operators
4.2.2 Passengers
4.3 Rail Safety
4.4 Conveyor Belts
4.5 Equipment Guards
5. persoNAL PROTECTIVE EQUIPMENT
5.1 Introduction
Hazards
5.2 Special Or Additional Personal Protective Equipment
5.2.1 Eye Protection
5.2.2 Face Protection
5.2.3 Hand Protection
5.2.4 Body Protection
5.2.5 Respiratory Protection
5.2.6 Fall Prevention Devices
6. SAFE MANUAL HANDLING
6.1 Introduction
6.2 Risk Assessment
6.3 Lifting
6.4 Manual Handling
7. HAZARDOUS SUBSTANCES
7.1 Introduction
7.2 Purchasing And Usage Control
7.3 General Safety Rules For Hazardous Substances
7.3.1 Safety Showers
7.3.2 General Safety Rules
7.4 Breaking Into Hazardous Substance Pipelines
7.5 Decontamination Of Equipment
8. WORK PERMIT, ISOLATION AND TAGGING
8.1 WORK PERMIT
8.1.1 Plant Access
8.2 Isolation
8.3 Safety Tagging
8.3.1 Personal Danger Tag
8.3.2 Testing and Jogging Tag
8.3.3 Out of Service Tag
9. SAFETY SIGNS AND TEMPORARY BARRIERS
9.1 safety signs
9.2 Temporary Barriers
10. WORK IN CONFINED SPACES
10.1 Introduction
11. HOT WORK
11.1 Hot Work Activities
11.2 General Precautions
11.3 Gas Cutting And Welding
11.4 Arc Welding
11.5 Grinding Operations
12. FIRE FIGHTING
13. ELECTRICAL SAFETY
13.1 Introduction
13.2 Access To Switchrooms
13.2.1 Definitions
13.2.2 Colour Coding
13.3 Colour Coding Tags
13.4 Residual Current Devices (RCD’s)
13.5 Authorised Electrical Equipment
13.6 Electrically Operated Power Tools
14. HAND TOOLS
15. WORKING AT HEIGHTS
15.1 General Rules
15.2 Fall PREVENTION
16. WORKING ON ROOFS
17. SCAFFOLDING AND LADDERS
17.1 Scaffolding
17.2 Ladders
18. LIFTING GEAR AND EQUIPMENT
19. CRANES AND HOISTS
19.1 All Cranes And Hoists
19.2 Mobile Cranes And Slinging Equipment
19.3 Personnel Work Box
20. ELEVATING WORK PLATFORMS (EWP)
21. FORK-LIFTS
22. HIGH FACES (BULK STOCKPILES)
23. EXCAVATIONS
23.1 Requirements
23.2 Hazard Identification
24. COMPRESSED GASES
24.1 Gas Cylinders
24.2 Compressed Air
25. ABRASIVE BLASTING AND PAINTING
25.1 Abrasive Blasting
25.2 Spray Painting
26. HIGH PRESSURE WATER JET CLEANING
27. EXPLOSIVE POWER TOOLS
28. ASBESTOS REMOVAL
29. WORK IN A HOT ENVIRONMENT
30. WORK IN ACCESS WAYS
31. WORKING ALONE
31.1 Introduction
31.2 What is “Working Alone”?
31.3 OSH Regulations 1996
32. DRIVER FATIGUE
32.1 PLAN YOUR TRIP – PLAN YOUR BREAKS
32.2 SIGNS OF DROWSINESS
32.3 REMEMBER
INTRODUCTION
This guide manual provides an overview of the way in which Symmetrical Group expect its people to conduct their work. It contains essential information and instruction on general occupational safety and health rules and practices that all personnel working for Symmetrical Group need to understand and apply. Please note that our clients site practices and procedures may vary, in the event the Symmetrical Groups standard practice or procedure is over and above our clients requirements the person with the discrepancy should contact their supervisor to gain permission to work to the lesser requirement, where a site has a higher requirements Symmetrical Group will adopt this practice.
Safe working conditions and personnel training form only part of the accident prevention program. It is only through the full and complete participation of all personnel that the continuous success of the accident prevention program will be achieved.
All parties involved with work have responsibilities for safety and health at work. This includes employers, employees, self-employed persons, contractors and others such as people who control workplaces, design and construct buildings or who manufacture and design plant.
Obligations relating to the safety of personnel on site can be described under two main headings:
- the statutory duties as required under State legislation and,
- Common Law duty of care.
Statutory and safety and health requirements are currently found in a number of Acts and Regulations. The main ones are:
- Occupational Safety and Health Act and Regulations
- Dangerous Goods Act and Regulations
- Workers’ Compensation and Rehabilitation Act.
- Mine Safety and Inspection Regulations
An employer must, as far as is practicable, provide and maintain a working environment where their employees are not exposed to hazards.
General duties require an employer to;
- provide a safe place of work;
- provide a safe system of work;
- provide and maintain a safe plant and equipment
- provide competent staff to manage and supervise the work and the employee;
- provide instruction and training.
All persons at work must take reasonable care for their own safety and health and avoid harming the safety and health of others.
General duties include:
- Following safety and health instructions;
- Using and taking good care of PPE and equipment;
- Reporting work-related injuries harm to health and hazards.
Compliance to Basic Safety Rules, procedures and directions from management is an obligation of all contractors and employees
Managers will address and correct all substandard performances in the workplace immediately, if possible. The manager must be fair and consistent by investigating, evaluating and enforcing compliance to safety in his/her area.
-
resolution Of Safety & Health Issues
When an employee discovers a safety or health issue in the workplace it should be reported to his or her Team Leader. The Team Leader will attempt to resolve the issue. If the Team Leader cannot resolve the issue it will be referred to the management for immediate action.
If an individual breaches a recognised safety standard or fails to improve after receiving a final warning, the Manager may recommend suspension, demotion or dismissal of the employee.
Where a contractor breaches the recognised standard of safety performance or fails to improve after receiving a warning the Responsible Officer may recommend suspension or dismissal of the contractor.
-
ON SITE EMERGENCY ARRANGEMENTS
It is Symmetrical Groups policy to ensure that our people are properly inducted on every site they work on to ensure they are familiar with all visual and audible indications at each site and be prepared to respond in an appropriate way.

ENSURE YOU KNOW WHAT TO DO, WHERE TO GO, WHO TO COMMUNICATE WITH AND WHAT ACTIONS ARE TO BE TAKEN IN AN EMERGENCY SITUATION.
-
Reporting A Serious Injury Or An Emergency Situation
If a serious injury or on-site emergency occurs, at any time, day or night, it must be reported promptly by dialing the relevant site emergency number.
Potential on-site emergencies include:
- Serious injury or illness,
- Fire,
- Hazardous substance release or spill,
- Environmental contamination,
- Vehicle accidents,
- Structural failure, damage,
- Severe weather conditions,
- Crime i.e. bomb threats or terrorism.
The effects of these conditions range from an emergency notification to a full evacuation of all personnel.
Most sites are equipped with formal alarm systems to alert persons on site that an emergency exists.

Note: All Work Permits are automatically suspended on the sounding of any alarm. All Work Permits must therefore be revalidated prior to work recommencing following the “All Clear” (if the site your on does not have a permit to work system your site representative should be contacted to ensure its safe to return to work).
Symmetrical Group personnel are to ensure they are aware of each sites muster and assembly areas during the site induction, During an evacuation you are to remain at the assembly area at all times unless directed otherwise by the Area Warden.
For more information on emergency actions, communications and site evacuation see Individual Site Emergency and Evacuation Procedures
-
ACCIDENT, INCIDENTS & HAZARDOUS CONDITIONS
-
Reporting & Investigating
All accidents/incidents i.e. injury, illness, process loss, property/equipment damage and environmental damage, near misses (an incident which could have resulted in an accident), and hazardous conditions (a condition with the potential to result in an accident) must be reported.
All Accidents/Incidents shall be investigated to ensure all steps are taken to prevent recurrence.
If you are in doubt about the need for reporting, seek advice from your Supervisor, Team Leader, Client Representative, Safety & Health Representative or a member of the OSH Team.
All injuries requiring first aid treatment must be reported to your Supervisor, Team Leader or Client Representative.
Qualified first aid personnel will provide First Aid treatment.

FAILURE TO FOLLOW SAFETY RULES COULD RESULT IN INJURY, OR AFFECT THE HEALTH OF YOURSELF OR OTHERS.
The following general safety rules serve as the basis for good safety behaviour:
- There are no unsafe jobs – only unsafe ways of doing them..
- Always follow instructions. If you are uncertain, ASK.
- Report all accidents and incidents for investigation to prevent a recurrence. .
- Report all substandard and hazardous conditions or practices.
- Never carry out work you are not authorised to do.
- Observe safety instructions of hazardous substances at all times. Ensure that you know the nature of the hazardous substances that you are working with and that you employ suitable handling, storage and disposal practices and correct use of Personal Protective Equipment.
- In designated areas, wear appropriate and approved items of personal protective equipment, and maintain this equipment in sound working condition Smoke only in designated areas.
- Alcohol and illegal drugs are not permitted on Symmetrical Group work sites or in work areas. (Drugs are defined as illegal drugs or prescription or non-prescription drugs that have the capacity to impair judgement or cause drowsiness).
- If your health condition requires you to take prescription medication that may effect your performance, you must inform your immediate supervisor.
-
Vehicles And Mobile Equipment
The following general rules apply to drivers of vehicles and operators of mobile equipment:
- Compliance with Western Australian Road Traffic Rules must be adhered to at all times.
- Do not operate mobile equipment unless you are competent or registered as a trained operator or under instruction from a competent, trained instructor.
- Comply with site speed limits at all times.
- Seat belts shall be worn, where fitted, in vehicles and mobile equipment.
- Employee’s and Contractors employed by Symmetrical Group working on clients site’s, must not drive any of the clients vehicles without authorisation from the client and their Symmetrical Group supervisor.
- Do not drive company vehicles and mobile equipment, unless authorised.
- Give way to pedestrians - they have the right of way at all times.
- Do not use “hand-held” mobile phones whilst driving vehicles or operating mobile equipment.
The following general rules apply to passengers in or on vehicles and mobile equipment:
- Do not ride on vehicles or mobile equipment, unless authorised and provided with passenger seats.
- Do not mount or dismount from a vehicle or mobile equipment when it is in motion.
- Do not ride on the trays, fenders, running boards, tops, bumpers, side-walls, tailgates or bonnets of any vehicle or mobile equipment.
- Keep clear of all vehicles and mobile equipment, unless involved in their operation or direction.
Do not climb through a rake of cars or carriages, whether moving or stationary, ensure you stay at least 6m away from all rail activities unless crossing at designated rail crossing areas.
The following general rules apply when working with or around conveyor belts:
- Use conveyor walkways or crossovers to cross conveyors.
- Before starting work on a conveyor, ensure that a Work Permit is obtained and that the conveyor is correctly isolated and tagged.
- All conveyors have safety trip wires (lanyards) for your protection. In an emergency, pull or push the trip wire to stop the conveyor drive.

NO EQUIPMENT OR MACHINERY SHALL BE OPERATED WITH THE SAFETY GUARDS REMOVED.
Ensure that the equipment safety guards are in the correct position before starting any equipment. Before any safety guards are removed (for example, for cleaning or maintenance) the equipment shall be correctly isolated and tagged.
On occasions when equipment may have to be operated without the normal safety guards in place (for example, during testing, maintenance or commissioning), temporary safety guards, which provide the same level of protection as the normal safety guards, shall be in place before starting the equipment.
-
persoNAL PROTECTIVE EQUIPMENT
Adequate personal protective equipment, which complies with Company Standards, shall be used to protect personnel on site from hazards.
The work permit for any task should specify any additional personal protective equipment requirements that are not part of the minimum standard for the operational area.
All personnel must comply with PPE requirements indicated on boundary barriers. (see Section 9, Safety Signs and Barriers).
Hazards
The nature of hazards in the workplace should be considered when assessing PPE requirements and may be identified as one, or a combination of the following:
- direct contact, projectiles, sharp or abrasive, objects, moving machinery;
- chemical - irritant, carcinogenic, systemic poison, sensitiser,
- biological - bacterial, parasitic, fungal,
- physical - noise, radiation, extreme temperatures, vibration, ergonomic/manual handling.
- Material Safety Data Sheets (MSDS) should be consulted to identify required PPE for chemical and biological hazards. Where there is any doubt contact the OSH Team.
The wearing of personal protective equipment required on Industrial sites is mandatory for employee’s and contractors. Minimum personal protective equipment requirements are as follows:
- safety helmet,
- steel toe safety footwear,
- approved safety glasses, with clear , transition or amber lenses only are to be worn inside plant areas where visibility is affected by poor light.
- Long-sleeved top fastened at the wrist and long trousers in plant areas.
-
Special Or Additional Personal Protective Equipment
In addition to the minimum level of personal protective equipment required by all personnel on site, special protective equipment may be required for specific tasks.

CONTACT LENSES CAN WORSEN THE EFFECT OF FOREIGN BODIES (DUST, LIQUID AND GAS) IN THE EYES. THEREFORE CONTACT LENSES ARE NOT RECOMMENDED.
Special protection for the eyes can be provided by but is not limited to:
- goggles i.e. when taking samples,
- special lenses i.e. oxyacetylene work.
- hoods i.e. where respiratory, eye and face/head protection is required.
Special protection for the face is provided by visors or face shields.
Special protection for the hands can be provided by wearing the appropriate gloves.
Special protection for the body can be provided by, but not limited to:
- chemical splash suits,
- fully encapsulating chemical suits,
- wet weather clothing,
- leather aprons,
- leather welding jackets,
- leather spats,
- disposable overalls.
Special respiratory protection can be provided by but not limited to:
- disposable dust/mist masks, (minimum of P2)
- half or full face, air purifying respirators,
- Self-contained Breathing Apparatus (SCBA),
- Supplied-air Breathing Apparatus (SABA),
- Emergency Breathing Apparatus (EBA),
- Escape Life Support Apparatus (ELSA).
Fall prevention devices are worn to prevent the danger from falling when working at heights. See Section 16 Working at Heights for acceptable equipment and correct usage.

FALL PREVENTION DEVICE MUST BE HARNESS TYPE AND SHOULD BE WORN AT HEIGHTS OF ABOVE 2 METERS AND ABOVE OR WHERE THERE IS A POTENTIAL OF A FALL OCCURRING.
In manual handling, the person is the prime source of power in moving materials and equipment. Manual handling includes lifting, pulling, pushing, carrying or moving.
Any manual handling task that is likely to be a risk to health and safety must be examined and assessed before the task begins. The assessment is done in consultation with the personnel involved in the manual handling task and takes into account;
- the force applied by the person,
- the actions and movements involved,
- the range of weights handled,
- duration and frequency of movements,
- time and distance over which an object is handled,
- the availability of mechanical aids,
- the layout and condition of the workplace,
- the work organisation,
- postural requirements imposed by the manual handling task,
- the skill, strength and the experience of the personnel,
- the nature of the object/material being handled,
- any other relevant factors.

35 KG IS THE MAXIMUM WEIGHT TO BE LIFTED. USE MECHANICAL ASSISTANCE AND OR TEAM LIFTING ARRANGEMENTS TO REDUCE THE RISK OF INJURY.
- The risk of back injury increases significantly when lifting weights heavier than 20 kg.
- When sitting, do not lift loads heavier than 4.5 kg.
- Do not lift loads heavier than 55 kg manually.
Use the following principles to ensure safe manual handling of materials and equipment:
- Before starting any manual task, assess the situation by sizing up the load, and:
- if the load is too heavy or awkward, lift with mechanical assistance or get help,
- ensure that the load is safe for handling (no sharp edges, protrusions etc),
- ensure that the area around the load is safe,
- check that the place the load is to be moved to is clear to accept the load,
- wear the appropriate personal protective equipment,
- Correctly position your body:
- position your body correctly before starting,
- bend your knees,
- grip the load firmly,
- keep your back straight,
- keep your body balanced,
- lift the load smoothly, using your legs - not your back.
- Handle the load correctly:
- use your body weight to move the load,
- face the direction in which the load is to be moved,
- hug the load close to your body,
- move your feet - do not twist your body,
- look where you are going,
- move slowly and steadily, do not jerk,

Figure 1 - Correct Manual Handling Operations
In this section the word “Hazardous Substance” refers to any chemical or material that has hazardous/toxic characteristics or properties (i.e. Asbestos, Solvents, Benzene, Acids and Alkalis)..
Exposure and/or environmental control measures must be evaluated and implemented. Control measures are introduced in the following hierarchy or order of preference:
- Elimination of the need for the hazardous substance.
- Substitution with a less hazardous substance.
- Engineering measures, such as enclosure and/or ventilation.
- Administrative measures, such as restricting access/exposure by job rotation.
- Use of personal protective equipment.
-
Purchasing And Usage Control
No hazardous substance shall be introduced to the workplace unless:.
- it has been approved for use, by the Directors of Symmetrical Group
- its use, presence or production is essential, and there is no alternative product or process available,
- applicable National Industrial Chemicals Notification and Assessments Scheme requirements are met,
- an approved Material Safety Data Sheet is available to those who will be handling or using the substance,
- all statutory and company requirements can be met for:
- Packaging,
- Labelling,
- Storage,
- Transport,
- Emergency procedures,
- Waste disposal and environment protection.
-
General Safety Rules For Hazardous Substances
Safety showers and eyewash stations are identified by green fluorescent light. Familiarise yourself with the location and operation of these showers in your own work area. If contamination occurs, irrigate the eyes and/or wash the contaminated area for at least 20 minutes under the shower. Remove contaminated clothing in the shower.
Hazardous substances shall be handled only by personnel properly trained in its use and protected by appropriate personal protective equipment.
MSDS and Job Safety Analysis shall be used to identify all potential risks. Note: All spills must be reported, cleaned up and or neutralised.
-
Breaking Into Hazardous Substance Pipelines
- Before starting work, the Work Permit Authoriser must ensure that all persons who are to work on the pipeline, and associated equipment or vessels have:
- Received instruction on the chemical properties of the hazardous substance concerned,
- Received instruction/training on the required PPE,
- Received instruction/training on relevant safe work practices and precautions to be taken,
- Obtained a Work Permit , and Special Permit if required,
- Dressed in the required PPE, or have the required PPE at hand, as appropriate.
- The Work Permit must include the precautions to be taken e.g.
- Location and testing of safety shower,
- Arranging to have running water available,
- Barricade area or posting a guard,
- Placement of warning signs,
- Appropriate PPE CLASS (1, 2, 3).
- When opening any pipeline by breaking a flange, the following precautions are to be taken:
- Work up-wind of the flange to be broken.
- Slacken the bolts on the far side of the joint first.
- Break the flange away from your body.
- Beware of a sudden release of fluid when and after the flange has been broken.
- Beware of flammable gas that may be released.
- Contain or collect any residual fluid and return it to the process.
- Clean away any spillage immediately.
- Wash and clean any tools and equipment used.
- Leave the job in a safe condition.
-
Decontamination Of Equipment
Many items of equipment such as pipes, valves and pumps are in contact with hazardous substances whilst in service. When these items need to be taken out of service for transportation and/or repair off site or on site, they must be decontaminated so that persons involved in the transportation or repair can handle them safely. This applies also to hire equipment that has been in contact with any hazardous substance.
-
WORK PERMIT, ISOLATION AND TAGGING

NO WORK OTHER THAN AUTHORISED PLANT/AREA ROUTINE WORK SHALL BE DONE WITHOUT AN ISOLATION.
On sites that use a Work Permit system the permit is generally the key document associated with the permit system. The Work Permit Authoriser is responsible for the management of the Work Permit; however other personnel also have responsibilities as defined in the Job Safety Analysis. The purpose of the Work Permit is to hand over the equipment in a safe condition to the Work Permit Holder doing the work to ensure the following:
- Personnel doing the work and others who may be in the vicinity of the work are not exposed to the risk of injury.
- The protection of machinery and equipment.
- Recommissioning the machinery and equipment in a controlled manner on completion.
The Work Permit Authoriser, as the person responsible for the operation of the plant, area or equipment shall be contacted before the work is started. This is done so that he/she is familiar with the task, the number of personnel involved and their location within the plant or area.
- For detailed information on the Work Permit System refer to the client’s procedure

ALL ISOLATIONS SHALL COMPLY WITH symmetrical groups SAFETY TAGGING SYSTEM. FAILURE TO DO SO WILL RESULT IN DISCIPLINARY ACTION
To ensure safe working conditions, the Symmetrical Group Safety Tagging System is used. In our system, we use a combination of three safety tags to prevent other personnel, who are not involved in the cleaning, inspection or repair work, from using the item of equipment or the system involved. These five tags are:
- Personal Danger Tag
- Testing and Jogging Tag
- Out Of Service tag

The Information Tag is not a safety tag and should not be used as such.

ONLY THE PERSON NAMED ON THE PERSONAL DANGER TAG IS PERMITTED TO REMOVE IT. REMOVAL OF ANOTHER PERSON’S TAG WILL RESULT IN DISCIPLINARY ACTION.
The Personal Danger Tag is used to protect the person named on the tag. Personal Danger Tags are used to indicate which personnel are working on the equipment and names those who could be put at risk if the equipment starts.
It is a warning to all personnel that the equipment shall not be operated until the tag has been removed by the person named on the tag.
Note: The Personal Danger Tag is red, black and white in colour and states “Do Not Operate”.
Testing and Jogging Tags are used when isolation has been de-isolated for the purpose of testing or jogging that equipment.
Note: The Testing and Jogging Tag is white with a green border.
The Out of Service Tag is used in the following circumstances:
- Reporting equipment that could cause injury or damage if operated.
- Reporting unsafe portable equipment (e.g. ladders and hand tools).
Note: The Out of Service Tag is yellow with a black diagonal stripe colour
For more information on Safety Tagging see Symmetrical Group Procedure Safety Tagging System and Symmetrical Group Procedure Equipment Testing and Jogging.
-
SAFETY SIGNS AND TEMPORARY BARRIERS
Standard safety signs are classified as a:
- regulatory sign,
- prohibition - red and white
- mandatory - blue
- warning sign - yellow and black
- emergency-related sign - red
- safety-related sign - green
Safety signs do not replace the need for proper accident prevention measures. Safety signs are provided to guide and protect all personnel from exposure to hazards. Observe and obey them at all times.
The following points shall be borne in mind when positioning signs:
- Signs shall be visible at all times.
- Prohibition, danger, obligation and caution/warning signs shall be sited on an approach to the hazard, far enough away from the hazard to allow ample time to read and heed the warning before arriving at the hazard.
- The number of signs at a location shall be limited to the least practicable number to ensure the effectiveness of signs in the area are not reduced.
Barriers shall be erected as necessary with signs to indicate to personnel the restrictions or actions required. Temporary barriers/isolation may be in the form of:
- bunting,
- portable metal frames,
- wire mesh fences,
- warning posts with chains, ropes or highly visible tapes,
- traffic cones,
- hazard lamps and beacons,
- floor marking.
The type of barrier chosen shall be appropriate to the circumstances: e.g. when work is being conducted overhead, floor areas and access ways are to be roped off and signs posted.
An Information Tag is to be attached to the temporary barrier, with all the necessary information indicated on the tag. The tag is to be removed when the information is no longer relevant.
Only personnel assigned to the work are permitted in a barricaded or roped off area. When they are no longer required, ropes and barricades shall be promptly removed.
Work in a vessel or other confined space requires particular safety and health considerations. Key concerns are the potential presence of toxic vapours, explosive atmospheres or oxygen deficiency. Other harmful agents, such as noise, mechanical equipment and heat are also a greater potential safety and health hazards in confined spaces.
Confined spaces include, but are not limited to:
- storage tanks, , process vessels, boilers,
- bins and other tank-like compartments, usually only having an access hole for entry,
- open-topped spaces, such as pump pits, hoppers, and chutes, which are not subject to good natural ventilation,
- pipes, tunnels, ducts and similar structures.
In each plant or area where there are specific confined spaces, a signed and dated list of those confined spaces is to be displayed in a prominent position in the control room.

ALL CONFINED SPACES SHALL BE TESTED FOR OXYGEN DEFICIENCY AND THE PRESENCE OF EXPLOSIVE GASES BEFORE ENTRY
ALL PERSONNEL REQUIRED TO WORK IN CONFINED SPACES SHALL BE TRAINED.
Hot work includes:
- any work which could generate sparks or heat of sufficient intensity to ignite combustible gases, liquids or materials within a hazardous zone.
Take the following general precautions when carrying out hot work:
- Assign a Fire Watch while hot work is in progress, and for at least 30 minutes after work is completed.
- Position appropriate fire extinguishers near sources of ignition.
- Sparks shall be contained by fire resistant blankets or similar.
- Prevent sparks from entering low-lying areas, such as drains.
- Use enclosures to ensure sparks from aboveground work do not enter hazardous areas on lower levels.
- Keep welding machines and gas cylinders at least 8 metres from low lying areas such as drains.
- Earth welding machines directly to the equipment being welded, as close to the welding point as possible.
- Do not drape power leads across pipelines or access ways.
- Switch off power sources at completion of work or during breaks.
- Isolate valves purge gas hoses and remove cutting equipment when work is suspended for any period.
- Locate welding machines and cylinders outside hazardous areas e.g. confined spaces..
For more information on Hot Work requirements see Symmetrical Group Procedure Hot Work.
The following precautions shall be taken when conducting gas cutting and welding:
- Gas cylinders, full or empty, not held or supported by a mobile trolley, shall be secured in an upright position to a suitable support using a non-flammable restraint.
- Cylinder neck threads shall be clean and oil-free. Compressed oxygen in contact with oil can cause an explosion.
- Oxygen and acetylene cylinders shall be stored separately.
- Oxygen and acetylene cylinder regulators shall be fitted with an approved flashback arrester when in use. Flashback arresters shall also be fitted to the hand piece.
- Cutting torches, blowpipes and tubing shall be well maintained and tubing must be colour coded in accordance with AS1345 (“Identification of the contents of piping, conduits and ducts”).
- In elevated areas barriers shall be erected to protect personnel in the area, and, where falling sparks could cause a fire or explosion, flameproof blankets shall be used to isolate the work from the surrounding area.
- The initial cut into an existing pipe system shall be a cold cut. A small hole is to be drilled first to confirm the pipe is depressurised. Hot work shall not commence until the entire pipe is confirmed safe.
- Flame cutting shall not be performed on colour bond sheet metal or similar products.
- Welding or cutting shall not be performed on drums, barrels or other containers, unless they have been proved free of flammable or explosive liquids or vapours. An authorised Gas Tester shall provide this proof.
- When not in use Cylinder valves shall be tightly closed and hoses purged.
- Oxygen or acetylene shall not be used to remove dust from clothes or work pieces.
- When using fall protection equipment and systems ensure that they are protected from all heat sources such as sparks. .

WET OR DAMP SURFACES GREATLY ENHANCE
THE LIKELIHOOD OF ELECTRIC SHOCK.
Take the following precautions when arc welding:
- Carry out arc welding only if you are authorised to do so.
- Keep work areas and equipment dry and clean at all times.
- To prevent stray arcs and sparks in other locations, attach an earth lead to the material being welded, at a location immediately adjacent to the welding.
- Hand pieces should be insulated.
- Do not leave energised electric rod holders unattended. Always remove the welding rod and turn off the power.
- Never wear wet clothing, wet gloves or wet footwear while welding.
- Switch off the power supply to the welding machine before connecting or disconnecting welding leads.
- Ensure the insulation on welding leads is in good condition.
- Keep welding cables clear of other personnel.
- Screen welding, cutting and gouging activities to protect other personnel working in close proximity from flashes and sparks.
For more information on welding and gas cutting see Symmetrical Group Procedure Hot Work (GM-11-036-05).

SAFETY GOGGLES SHALL BE THE MINIMUM EYE PROTECTION WORN FOR ALL GRINDING OPERATIONS.
The following precautions shall be taken when grinding:
- Angle grinders and pedestal grinders/buffers shall not be used unless they are fitted with suitable guards.
- Bench and pedestal grinders shall be provided with a protective shield of Perspex or armour glass over the wheel to prevent sparks or metal hitting the operator.
- All hand-held grinders shall be fitted with a dead man (on/off) switch.
- Respiratory protection shall be worn when grinding or cutting magnesium, aluminium and aluminium bronze, the metallic dust from which can be hazardous.
-
FIRE FIGHTING
Portable fire extinguishers are intended as first attack devices for fires of limited size.
Fire hydrants, hoses, hose reels and associated equipment designated for emergency use shall not be used for any other purpose.
All personnel shall be trained in the use of fire fighting equipment.
|
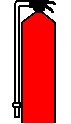
|

|

|

|

|

|
A
Ordinary Combustibles (Wood, Paper, Plastics)
|
yes
Most Suitable
|
Yes
|
YEs
|
Yes
ABE
NO
BE
|
No
|
Yes
|
B
Flammable And Combustible Liquids
|
no
|
no
|
yes
|
yes
|
yes
|
yes
|
C
Flammable Gases
|
no
|
no
|
no
|
yes
|
no
|
no
|
E
Fire Involving Energised Electrical Equipment
|
no
|
no
|
no
|
yes
|
yes
|
yes
|
F
Fire Involving Cooking Oils And Fats
|
no
|
yes
|
yes
|
no
ABE
yes
BE
|
yes
Limited Effectiveness
|
no
|
Figure 2 - Fire Extinguishers

ALL ELECTRIC SHOCKS MUST BE REPORTED AND MEDICAL TREATMENT RECEIVED (ECG).
ALL ELECTRICAL INJURIES MUST BE REPORTED TO THE OFFICE OF ENERGY BY THE COMPANY DESIGNATED OFFICER.
Electricity is a hazard that cannot be sensed until contact is made. Current flow is the component of electricity that injures personnel.

Figure 3 - Electrical Current Flow
To protect personnel and equipment, a number of controls and safety requirements have been established on site.
Only authorised personnel shall carry out work on or switch on any circuit connected to the electrical system.
Only personnel who hold a current, appropriate Western Power Electrical Worker’s Licence are authorised to remove or change fuses.
Non-licensed personnel shall not enter any switch room, motor control centre or rear of control panel where there is direct access to live parts at a voltage above extra low voltage. Authorised personnel (e.g. Operators, Mechanical Fitters, and Instrument Fitters etc.) are permitted to enter switch rooms when there is no direct access to live parts.
Extra Low Voltage
|
Voltage not exceeding 32 volts AC or 115 volts DC (typically 24 or 48 volts DC).
|
Electrician
|
Person who holds a current “A” Grade Electrical Mechanics License.
|
Authorised Personnel
|
Persons authorised to access areas as necessary to perform duties in line with their responsibilities provided that at all times the person shall not place themselves at risk or contravene regulations or directives or Statutory Authorities with jurisdiction over the areas.
|
Switch room
|
Any room containing electrical equipment that is used to distribute electrical power or control electrical motors.
|
A colour coded tag system is used to ensure that all portable electrical equipment and flexible extension cables (extension leads) are inspected quarterly or annually as required following the initial safety inspection and registration.

Only portable electrical equipment and flexible extension cables with the current colour coded tag shall be used.
The colour code tag requirements are as follows:
TESTING INTERVAL
Testing intervals for electrical equipment are as follows.
TYPE OF ENVIRONMENT IN WHICH EQUIPMENT IS USED
|
TEST INTERVALS
CLASS I (PROTECTIVE EARTH)
|
TEST INTERVALS
CLASS II (DOUBLE INSULATED)
|
TEST INTERVALS
EXTENSION LEADS AND EPOD'S
|
Type 1
Factories, workshops, places of repair manufacturing, assembly, maintenance or fabrication.
|
3 months
|
3 months
|
3 months
|
Type 2
Laboratories, health care and educational establishments, tea rooms, office kitchens, hotels and motel accommodation.
|
12 months
|
12 months
|
12 months
|
Type 3
Office environment where equipment is not subject to constant flexing of the supply cord.
|
5 years
|
5 years
|
5 years
|
Table 1 - Testing Intervals for Electrical Equipment
COLOUR CODING
Portable electrical equipment tags shall be coloured coded as follows.
ENVIRONMENT TYPE
|
PERIOD
|
COLOUR
|
Type 1
Factories, workshops, places of repair manufacturing, assembly, maintenance or fabrication.
|
January - March
|
Red
|
April – June
|
Green
|
July - September
|
Blue
|
October – December
|
Yellow
|
Type 2
Laboratories, health care and educational establishments, tea rooms, office kitchens, hotels and motel accommodation.
|
January - December
|
White with Black lettering
|
Type 3
Office environment where equipment is not subject to constant flexing of the supply cord.
|
Table 2 - Colour Coding - Portable Electrical Equipment & Flexible Extension Cables
Electrical equipment and flexible extension cables that are suspected of being defective in any way must not be used until the defect has been corrected.
If an electrical defect is identified or suspected an “Out of Service Tag” is to be attached and repairs by an authorised repair person arranged.
-
Residual Current Devices (RCD’s)
Protection against earth leakage current is mandatory when portable electrical equipment is in use. This does not apply when the supply of electricity:
- Does not exceed 32v alternating current,
- Is direct current,
- Is provided through an isolating transformer complying with AS/NZS3108, or
- Is provided from the unearthed outlet of a portable generator.
RCD’s are normally set to function at 30 milliamps. Employees and Contractors are responsible for providing portable RCD protection whenever they connect into a power source on a Symmetrical Group work site not RCD protected.
-
Authorised Electrical Equipment
When work is to be done within the plant, the correct type of electrical equipment specified by the electrical authorising officer shall be used and all necessary safeguards taken.
-
Electrically Operated Power Tools

ALL POWER TOOLS USED IN CONFINED SPACES SHALL BE FITTED WITH DEAD MAN (ON/OFF) SWITCHES.
ELECTRICALLY OPERATED POWER TOOLS SHALL NOT BE USED IN WET AREAS UNLESS PRECAUTIONS ARE TAKEN TO PREVENT MOISTURE CONTACTING LIVE PARTS.
The maintenance and adjustment of electrically operated power tools, needs specialised knowledge. Problems shall be reported to your Team Leader or Responsible Officer immediately and arrangements made for an electrician to carry out inspections/repairs. Take the following precautions when using electrically operated tools:
- Use a portable RCD for 240-volt portable electric tools and equipment to protect against electric shock when built in RCD protection cannot be proven.
- Plug the portable RCD directly into the general-purpose outlet so that flexible extension cables and tools are protected. Do not, under any circumstances plug the RCD into the socket end of a flexible extension cable.
- 10 Amp flexible extension cable runs shall not be more than 30 metres in total length and shall be fully unwound to prevent overheating. Do not connect more than two flexible extension cables together.
- Where RCD’s are permanently fitted to the main electrical supply, portable RCD’s are not required.
For more information on electrical safety requirements see Symmetrical Group Procedure Portable Electrical Equipment).
Use the correct tool for the job. Select the weight, size and type of tool to suit the job being done, and take the following precautions:
- Check that handles are securely fitted to tools.
- As most hand tools conduct electricity, exercise extreme caution when working near electrical equipment.
- Regular checks of insulated and non-conducting tools (e.g. pliers and screwdrivers) must be conducted to ensure they are in good condition.
- Do not leave tools on walkways, aisles, stairways or elevated places.
- Ensure all hand tools are in good condition and appropriate for the task being performed.
-
WORKING AT HEIGHTS
Take the following precautions when working at heights to prevent the danger from falling:
- Wherever practicable, position personnel behind permanent or temporary physical barriers.
- Reassess work procedures to permit personnel to work behind barriers in preference to using fall prevention systems.

When it is a requirement to work at heights of 2 metres or more without permanent or temporary barriers a JOB SAFETY analysis must be undertaken which is to be approved by the client representative prior to the work commencing.
- Acceptable alternatives to physical protection against falling include:
- Safety harness and lanyard,
- Inertia reel and harness,
- Crane work box,
- Elevating work platform,
- Swing stage scaffold/suspended scaffold.
- Scissor Lift
- Only use safety equipment that is clearly free from defects.
- Check for damaged assembly and function before trusting weight to safety equipment, such as safety harness, inertia reel or anchorage points.
- Beware of high winds when working exposed at heights.
For more information on working at heights see Symmetrical Group Procedure Safe Working at Heights.
When it is necessary to work at heights at or above 2 metres and permanent or temporary barriers are not provided, fall protection is mandatory.

Working at heights of less than 2 metres can also present a fall hazard. If there is a risk of falling, fall prEVENTION must be provided
Observe the following rules when using fall protection equipment:
- When using fall prevention systems, ensure that components such as inertia reels are attached to a suitable anchorage point that is free from sharp edges, and is capable of taking the full force of a fall. ( Safety handrails shall not be used as anchorage points)
- Only a full body parachute type harness is to be used for fall arrest.
- Fit and use safety harnesses correctly in accordance with manufacturer’s instructions, and adjust properly to reduce slack.
- Lanyard assemblies are to be the shortest practical length (maximum length of 2 metres), have a built in energy absorber and must be withdrawn from service and destroyed if used to arrest a free fall.
- Keep the slack in the safety line, between the person and point of anchorage, to a minimum.
- Anchor the inertia reel and lanyard assembly as high as the equipment or task permits.
For more information on fall protection equipment see Symmetrical Group Procedure Fall Prevention Equipment.

ONLY AUTHORISED PERSONNEL ARE PERMITTED ACCESS TO ASBESTOS and FIBROLITe roofs or a metal roof WHERE THE CONDITION OF THE ROOF IS UNSOUND OR SUSPECT. JOB SAFETY ANALYSIS SHALL BE DONE OBTAINED BEFORE ACCESSing any ROOF.
The following precautions shall be taken when working on roofs:
- Where the risk of falling and/or where there is no roof protection only personnel wearing approved fall arrest equipment are permitted access to roof areas and then only for light work or for a short time.
- Roof ladders or properly fixed crawling boards shall be used for all work on sloping roofs with a pitch of over 30?.
- For work on roofs with pitches greater than 50?, or curved roofs, scaffold platforms shall be used.
- Personnel shall only work within areas protected in one of the following ways:
- Bounded by roof edge protection,
- Bounded by personnel barriers placed across the roof,
- Where two anchor points are provided,
- Where an inertia reel provides a safe range of movement and does not allow a person to come close to the edge of the roof.
- Rails shall adequately guard roof openings within the roof area.

Hazards associated with working on roofs may be increased
by rainy, hot, or windy conditions.
For more information about working on brittle roofs, see Symmetrical Groups Procedure Safe Working on Roofs.
All scaffolding and associated equipment used on site shall comply with statutory requirements.
Scaffolding shall not inhibit the proper operation of or access to safety and production equipment. Positioning of boards and staging supports shall be planned so as not to obstruct access on walkways, fire equipment, eyewash and emergency showers, emergency shutoff or shutdown devices and alarm panels.
For more information on work in access ways see Section 31 and Symmetrical Group Procedure Safe Working in Access Ways.
The following rules apply when working with scaffolding:
- Scaffolds shall display a “Scaff Tag” to indicate scaffold status.
- Scaffolds over 4 metres shall only be constructed, altered or dismantled under the supervision of a licensed scaffolder.
- Stages or swing scaffolds shall not be suspended from channel iron clamps.
- Scaffolds 2 metres or more in height shall be fitted with fender or kick boards and guard rails.
- Planks shall not overhang their supports by less than 150mm or more than 250mm except where the plank is overlapped.
- All scaffold planks shall be lashed or pleated.
- Every scaffold shall have an access such as a ladder. When a ladder is used it must project at least 1 metre beyond the working platform or landing.
- Safe access to and safe egress from the scaffold must always be considered and provided for.
Observe the following rules when using ladders:
- Only use portable ladders as a means of access or for light duties of short duration.
- When working at heights fall protection shall be used.
- Do not use drums or makeshift pieces of equipment to climb up or down.
- Inspect ladders frequently and rectify defects immediately.
- Ensure that the foot of the ladder is on a firm, level surface and at a safe distance from the vertical (1 metre for every 4 metres vertical).
- Ladders are to be secured in place by tying.
- An attendant shall be stationed at the foot of the ladder when required.
- When using extension ladders, always have at least four rungs overlapping at the centre of the ladder.
- Ensure that ladders protrude at least 1 metre above the platform/surface against which they are resting.
- Always face the ladder and use both hands when ascending and descending. ( maintain 3 points of contact)
- Always use a line to raise or lower tools and equipment from a height.
- Do not use aluminium ladders in areas where they may come into contact with live electrical conductors.
For more information about scaffolding and ladders see Symmetrical Group Procedure Scaffolding, Planks and Ladders.
-
LIFTING GEAR AND EQUIPMENT

LIFTING GEAR AND EQUIPMENT SHALL BE VISUALLY INSPECTED FOR WEAR, STRETCH AND DEFECTS BEFORE USE. NATURAL FIBRE ROPES, SUCH AS SISAL ROPES ARE NOT TO BE USED ON SITE.
Take the following precautions when using lifting gear and equipment:
- Check hooks for opening out.
- Do not overload - never use additional power or leverage on any hand chain, handle, wire rope or sling.
- Do not throw or drop lifting gear and equipment.
- Protect chains, wire ropes and slings from sharp corners.
- Never apply heat to chains, hooks, wire ropes or slings.
- Do not cross, twist, knot or kink chains.
- Do not use chains, which show more than 10% wear in the links or where the links are extensively pitted.
- After use, lifting gear and equipment shall be cleaned and stored in a dry place, free from chemical contamination.
- Wire ropes and slings shall not be used if any defects such as distortion, crushing, broken wires or damage to ferrules, thimbles, hooks etc. are observed.
- Chain slings shall be checked to ensure they are clearly marked with the safe working load (SWL).
- If a chain, wire rope or sling has been subjected to shock or impact loads, carefully examine the equipment before returning it to service.
- Do not use a chain in which the links are locked, stretched or without free movement. Do not hammer a chain to straighten a link or to force a link into position.
- Do not use flat web slings to raise, lower or suspend a load.
- Do not drag chains and slings from under a load. Support the load to allow easy removal of slings.
- Do not leave chains, wire ropes and slings on lifting hooks when not in use.

DO NOT WORK OR PASS UNDER A SUSPENDED LOAD
KEEP WELL CLEAR OF SUSPENDED LOADS
For more information about Slings, Rigging and Lifting requirements see Symmetrical Group Procedure Rigging and Lifting Equipment Safety.
Conditions and requirements for the operation and use of all cranes and hoists shall be in accordance with the WorkSafe WA Occupational Safety and Health Regulations. Operators of cranes shall be licensed.

CRANES SHALL NOT BE OPERATED CLOSER THAN 6 METRES TO ANY OVERHEAD PIPELINE OR ELECTRICAL CONDUCTOR WITHOUT APPROPRIATE SAFEGUARDS.
The following precautions shall be taken when working on or around cranes and hoists:
- Cranes shall only be operated by authorised persons who have received the required training for the class of crane used.
- Crane operators shall not lift a load beyond the rated capacity of the crane hoist, nor shall the maximum permissible working load on any hook, sling, chain or rope used for the lifting of loads be exceeded.
- No person shall board or leave the cab of a travelling crane until it is stationary.
- Climbing along crane rails is prohibited except by authorised personnel carrying out inspections or maintenance work.
- Crane operators shall not leave the crane unattended when;
- Power is onto the crane,
- There is a suspended load, or
- When slings, chains or ropes are under tension.
- Faulty slings and lifting equipment shall be tagged with an Out Of Service tag and returned to the Team Leader of the area for repair, exchange or disposal.
-
Mobile Cranes And Slinging Equipment
Take the following precautions when working on or around mobile cranes:
- Do not stand too close to a mobile crane cab as a shear point exists between the cab and the chassis of the crane.
- While a crane is operating, do not stand within the radius of the jib and its load unless you are working with the crane.
- Check all slings for defects before using them. Slings that are damaged, kinked, burnt or have broken strands shall not be used. They shall be destroyed.
- When a lift is being undertaken, stand well back in case a load is not properly centred.
- Do not walk or stand under suspended loads.
- One person only shall give a crane driver signals. (See Figure 5 for crane hand signals).
- No person shall ride on a crane boom or load.
- Use tail ropes where necessary to control material while it is in the air.
- Protect finished surfaces from damage by lifting equipment, and protect all lifting equipment from sharp corners and edges.
- Do no exert a sideways pull on a shackle or eyebolt.
- Eyebolts are to be thoroughly inspected by a competent person prior to being used to lift equipment electric motors, gearboxes, switchgear and the like; by their eyebolt.
- If there is any doubt that the eyebolt is original, it should not be used as a lifting point.
Before a workbox is used in conjunction with a crane to lift personnel, a workbox special permit shall be completed, and all the conditions on the permit complied with.
For more information on mobile cranes see Symmetrical Group Procedure Mobile Crane Safety.

Figure 4 - Crane Hand Signals
-
ELEVATING WORK PLATFORMS (EWP)
Personnel authorised to operate an EWP shall comply with the following safety requirements:
- No person other than the authorised operator shall travel on an EWP while it is in transit.
- An EWP shall not be driven on any road unless the beam is first placed and secured in a stable position.
- An EWP shall only be operated on a firm surface with outriggers, where fitted, extended.
- An EWP shall not be operated on a grade or side slope beyond the limits of the fitted inclinometer.
- An EWP shall only be driven with the boom in line with the direction of travel.
- When using the reverse gear, high speed range shall not be used.
- The operator shall face the direction of travel.
- An EWP shall only be used to position personnel, their tools and equipment. The EWP shall not be loaded and operated in excess of its rated platform load capacity nor used as a crane.
- Exiting the working platform in an elevated position shall only be done, using a double lanyard hook-up system.
- An EWP shall not be operated closer than 3 metres from an exposed electrical conductor.
- Personnel working on the platform shall keep their feet on the platform floor. At all times they shall wear an approved safety harness, attached to an approved anchorage point . Anchor points should be located at the bottom of the work platform.
For more information on elevated work platforms (EWP) see Symmetrical Group Procedure Elevated Work Platforms.
Personnel involved in the operation of fork-lifts shall comply with the following safety requirements:
- Only authorised operators, trained to NOSHC 7019 Standard assessment, are permitted to use fork-lifts.
- If a fault or condition results in a fork-lift being dangerous to operate, it shall not be used until the problem is rectified.
- The operator shall conduct a pre-start inspection to check that the fork-lift is mechanically sound.
- No unauthorised alterations or adjustments to fork-lifts shall be made.
- Seatbelts shall be worn.
- Warning lights shall be kept flashing when a fork-lift is in use.
- A fork-lift shall not be used for jobs that it is not designed for.
- Personnel can only be lifted by means of an authorised work box.
- Keep fork-lifts clear of live electrical equipment.
- To prevent dangerous concentrations of LPG, which is heavier than air, LPG fuelled fork-lifts shall not be parked near pits.
- Only specially certified fork-lifts are to be used in the Ammonia/AN area.
-
HIGH FACES (BULK STOCKPILES)
Personnel are not to enter storage bins or stockpile areas without prior approval from the sites client representative.
When approval is granted Symmetrical Group employee’s and contractors will take the following precautions when working with high faces:
- Personnel on foot shall not approach any dump face higher than 2 metres.
- Personnel working in the vicinity of any dump face higher than 2 metres shall leave a clearance equal to the vertical height at all times.
- Front end loader drivers shall not work on a vertical dump face which is higher than the extended height of the machine bucket.
- Where a product is to be dug from the wings, and the dump height is greater than that of the extended machine bucket, a ramp shall be constructed.
- An agreed procedure is to be formulated before dump faces of more than 2 metres are brought down.
- Stacks of bulk material shall be built to lean inwards.
For more information on working high faces see Symmetrical Group Procedure Safe Working with Bulk Stockpiles and High Faces.
-
EXCAVATIONS
- All excavations to a depth greater than 150mm require a Special Permit authorised by the Field Engineering Designate.
- To identify excavation hazards an Excavation Checklist is to be completed by the Client Representative controlling the work.
- Machine excavation is not permitted within 1 vertical metre of existing or identified services and existing services are to be fully exposed and identified using hand excavation only.
- Excavations to a depth of 1.5 metres or more are to be in accordance with Subsection 6 A of the Workplace W.A. Regulations.
- The excavation site is to be barriered to prevent unauthorised entry.
In the event that any of the following listed hazards are identified, work must cease immediately and corrective action taken to remove or eliminate the hazard:
- Workers in an unsupported trench more than 1.5 metres deep.
- Excavated material, pipes, tools or timber too close to the edge of the trench.
- Cracks near and parallel to the edge of the trench.
- Subsidence alongside the trench.
- Water swelling or the uplift of the trench bottom.
- Surface soil falling into the trench.
- Workers climbing on trench support timbers.
- Machines moving too close to the edge of the trench.
- Trench in or near previously dug ground.
- Nearby machines causing vibration.
- Undercut trench sides.
- Water entering trench.
- Worker in trench outside the support system.
- Nails or spikes sticking out of timber.
- Gas pipes in poor condition near trench.
- Close proximity to existing building and support footings.
- Loads supported by waling.
- Scaffolding that does not conform to standard.
For more information on excavations see Symmetrical Group Procedure Excavation.
Take the following precautions when working with gas cylinders:
- Do not use cylinders unless you are sure of the contents.
- Do not drop cylinders from a height, or allow them to fall over.
- Cylinders are not to be lifted or lowered by mechanical means unless, they are contained in an appropriate type of box, or attachments are used suitable for the task being performed.
- Secure cylinders against movement and falling while in use, storage or transport.
- Do not allow any form of heating that would raise the temperature above 45?C.
- Do not use cylinders as rollers or supports.
- Protect cylinders from impact damage or the uncontrolled release of its contents while the cylinder is being used, moved, or stored.
- Protect cylinders from paint spray, acids, alkalis and prolonged water contact.
- Ensure no electrical power can flow through a cylinder, for example from arc welders.
- Do no attempt to repair cylinder valves.
- Keep cylinders, and in particular the valves, clean and free from grease and oil.
- Do not use cylinders with dirty valves.
- Do not attempt to clean valves, other than cracking the valve to clear the connection point (before fitting regulators).
- Close cylinder valves when cylinder is not in use and especially when the cylinder is empty.
- Tag discharged cylinders, prominently mark them “MT” and store in a separate, dedicated area for return to the supplier.
See Figure 6 for gas cylinder colour codes.

Figure 5 - Gas Cylinder Colour Codes

BECAUSE OF A DANGER OF SERIOUS INJURY COMPRESSED AIR SHALL NOT BE USED TO BLOW DUST, DIRT OR PARTICLES FROM THE BODY OR HAIR, OR FOR PERSONAL CLEANING PURPOSES OF ANY NATURE.
Take the following precautions when working with compressed air:
- Do not use compressed air for practical jokes or skylarking. It is dangerous and strictly prohibited.
- Do not use compressed air exceeding 200 kPa at the outlet for cleaning down machines. Using compressed air to clean down must be conducted under controlled conditions.
- Only use air hoses of the approved type, fitted with the approved connection and safety hose clamps.
- Only use air hose connectors that are fitted with safety clips/pins.
- Appropriate eye protection shall be worn when using compressed air.
For more information on safe use of compressed air see Symmetrical Group Procedure Compressed Air Safety.
-
ABRASIVE BLASTING AND PAINTING
The following precautions shall be taken when using abrasive blasting:
- Blast cleaning shall not be applied to surfaces containing asbestos.
- Before abrasive blasting to remove painted surfaces commences the paint shall be checked for lead content. If the paint is found to be lead based, proper environmental clean up and disposal of abrasive materials shall be put in place.
- On sites sensitive to garnet blasting where possible, wet blasting shall be used in preference to other types of blasting.
- A positive, fast acting emergency cut-off device (dead-man control) shall be fitted to the abrasive blasting hose to automatically cut off the flow of abrasive material from the blast pot if the person operating the nozzle becomes unable to control the flow of abrasive material through the nozzle. The person operating the nozzle shall be physically in control of the emergency cut off device on the abrasive blasting hose.
- Ball valve type controls are not automatic and shall not be utilised as an emergency cut-off device.
- The operator is to have control of the flow of abrasive material thought the nozzle.
- Where respiratory protection is required, a dedicated supply of breathing air shall be provided for the operator.
- Dry abrasive blasting shall only be carried out by an approved contractor. Silica abrasive materials shall not be used.
- Dry blasting shall be performed outside normal working hours unless special arrangements are made and the area can be effectively isolated.
- All possible precautions shall be taken to limit the drift of dust. Wind direction, and changes in wind direction, must be considered. (or containment of dust)
- Personnel working close to the abrasive blasting area shall be notified of the operation.
- The abrasive blasting area must be barricaded/roped off and sign-posted to warn unauthorised personnel not to enter.
- Short-term entry is acceptable if approved eye protection and respiratory dust protection is worn.
- Abrasive blasting hoses shall not pass near hazardous areas since sparks, due to static build up, could ignite flammable vapours.
- The abrasive blasting area shall be cleaned and damped down at the end of each work day to prevent risk of inhalation of dust, eye injuries, equipment damage and drains from becoming blocked.
- Long sleeved shirt and trousers or overalls and appropriate safety equipment, that is blasting hood, disposable overalls, gloves, safety footwear and individual ear and respiratory protection shall be worn. Disposable overalls shall have elasticised or be taped at the ankles, cuffs and collar to exclude grit and dust. All personnel in the vicinity of the operation shall wear goggles for eye protection.

ALWAYS ENSURE GOOD VENTILATION WHEN SPRAY PAINTING IN CONFINED AREAS
The following precautions shall be taken when spray painting:
- The area shall be screened off and preventative measures taken to prevent spray drift affecting areas outside the work area.
- Operators and others in the immediate vicinity shall wear approved respiratory devices.
- When working at height, an approved work platform shall be used and the area below marked with warning notices, or protected by the use of suitable sheets.
- When working at height, hoses shall be securely fastened to the scaffold.
- Spray painting pressures shall not exceed the maximum specified by the manufacturer.
- Discard paint-soaked rags in fireproof metal containers to prevent the risk of spontaneous combustion.
For more information about abrasive blasting and spray painting, see Symmetrical Group Procedure Blasting and Spray Painting Safety.
-
HIGH PRESSURE WATER JET CLEANING

ANY PERSON STRUCK ON THE SKIN BY A HIGH PRESSURE WATER JET SHALL RECEIVE IMMEDIATE MEDICAL ATTENTION. INTERNAL INJURY MAY BE MORE SEVERE THAN IS APPARENT AT THE SURFACE.
High pressure water jet cleaning involves using water discharge from nozzles at pressures above 13.6 bar and up to 1000 bar.
Personnel required to operate high pressure water jet cleaning equipment shall be trained, by a competent operator, in the correct use of the equipment to be used.
The following precautions shall be taken when using high pressure water jet cleaning:
- As well as the minimum PPE, face shield, goggles, gloves and wet weather PVC (overalls or jacket and trousers) shall be worn when using high pressure water jet equipment.
- Personnel shall not be permitted to work alone when using water pressures above 200 bar.
- Safety signs and a substantial barrier shall be placed at least 6 metres from the cleaning area.
- Pressure equipment shall be earthed before work starts and during operation, to prevent the development of electrostatic charges between the lance and the workplace.
- Pressure cleaning equipment shall be fitted with activating devices that require positive effort by the operator (hand or foot), to keep the supply valve open (dead man control).
- Dead man controls shall not be tampered with or modified under any circumstances.
For more information on high pressure water cleaning see Symmetrical Group Procedure Hydrojetting Safety, and Use Of High Pressure Water Equipment).

BEFORE ANY HAND-HELD EXPLOSIVE POWER TOOL IS USED, IT SHALL FIRST BE ESTABLISHED THAT THE WORK IS SUITABLE FOR THE FASTENERS.
Personnel involved in the operation of explosive power tools shall comply with the following safety requirements:
- Before starting work, appropriate barriers and signs shall be erected and shall be clearly visible.
- Unauthorised personnel shall be kept out of the work area.
- Shields shall be erected in the work area to minimise the risk of possible ricochets.
- Explosive-powered hand tools shall not be loaded until immediately before use. If there is a delay, they shall be unloaded before being laid down.
- Fasteners shall not be driven into brittle or hard material such as glazed brick, tiles, terracotta, granite, slate, glass or onto hard steel.
- All cartridges and fasteners shall be used strictly in accordance with the manufacturer’s specifications and requirements.
- Misfires shall be dealt with strictly in accordance with manufacturer’s instructions.
For more information about explosive power tools, see Symmetrical Group Procedure Safe Use of Explosive Powered Tools.

ASBESTOS CEMENT SHEETING IS SLIPPERY WHEN WET - HANDLE WITH CARE.
Personnel involved in the removal of asbestos cement building products shall ensure that the work is undertaken in accordance with both company and statutory requirements.
Take the following precautions when involved in asbestos removal:
- All personnel working in asbestos sheeting removal areas shall wear disposable overalls and approved disposable mask, or half mask respirator fitted with a dust cartridge approved for asbestos removal.
- Barricade the work area, and post with appropriate safety signs to prevent other personnel from entering.
- Spray asbestos cement sheets with polyvinyl acetate (PVC solution) or wet with water, and keep wet during removal.
- Remove asbestos sheets with the least possible breakage and without the use of power tools, except for the removal of fastening screws.
- Correctly wrap and seal all asbestos waste and remove from site to an appropriate storage place.
- Remove asbestos cement residue using an approved vacuum cleaner.
- Wash yourself thoroughly, before eating, going to the toilet or leaving the site.
- Food is not to be consumed in the process area.
For more information about asbestos removal, see Symmetrical Group Procedure Asbestos Cement Building Product Removal.
-
WORK IN A HOT ENVIRONMENT

PERSONNEL WHO EXPERIENCE PROFUSE SwEATING, OR FEEL CLAMMY, TOGETHER WITH DIZZINESS, MAY BE SUFFERING FROM DEHYDRATION AND SHOULD IMMEDIATELY SEEK MEDICAL ASSISTANCE.
The following safety precautions shall be taken when working in a hot environment:
- Cool drinking water shall be available at the work site in hot conditions, and employees shall be encouraged to take small, frequent drinks to keep pace with sweat loss.
- If affected by heat cramps, which normally only occurs under the severest heat stress conditions, seek medical attention immediately. In heat stress conditions the alternatives of work rescheduling, cooling and other preventative methods shall be employed.
- Work sites in localised areas in direct sunlight shall be shaded as much as practicable.
- Personnel working for extended periods in direct sunlight shall wear broad-brimmed hats, or attachments to safety helmets, and sun block creams to protect the skin. Where practicable, long trousers and long-sleeved shirts shall be worn to provide additional protection.
- Personnel working in the same location for extended periods shall request fixed umbrellas to provide shade.
- Personnel shall take adequate drink and rest breaks as dictated by the ambient conditions.
For more information about working in a hot environment see Symmetrical Group Procedure Safe Working In A Hot Environment.
When employees are required to remove part of a deck, grating, railing or stair to gain access, or for other reasons, the following are required:
- The agreement of the person responsible for the area.
- A safe, alternative access way, if required.
- Barriers across all approaches to the affected areas, with explanatory Information Tag attached and danger signs displayed.
- All other work levels to be considered in planning the work.
- The securing of scaffolding railings (to provide a physical barrier to entry) is to be included in the Work Permit requirements.
- A satisfactory inspection before work starts.
On completion of the work:
- The area shall be checked to ensure that all removed sections have been replaced, and all equipment, barriers and signs have been removed.
- The Work Permit (PF0421) shall not be signed off until the above has been completed.
For more information about working in access ways, see Symmetrical Group Procedure Safe Working in Access Ways.
The risk of injury or harm for people who work alone may be increased because of difficulties contacting others when assistance is required.
Emergency situations may arise because of the sudden onset of a medical condition; accidental work related injury or disease; exposure to hazardous substance. The consequences may be very serious and the injury or disease may be fatal.
A person is alone at work when they are on their own; they cannot be seen or heard by another person; and they cannot expect a visit from another person for some time. The minimum time a person has to be on his or her own for the person to be considered “alone” has not been set and each situation must be assessed on its merits.
For example a worker is alone when he or she:
- Works in a depot or site where there are no other employees,
- Works in a workplace when everyone else has gone home,
- Undertakes maintenance in a vacant or dead plant,
- Is called out at night to check on a security alarm when others are not present.
People who have regular contact with others as part of their work are not alone in this context.
Safe Systems of Work for people who work alone should take various parts of the OSH W.A. Legislation into account. This would include the General Duties Of Care and the specific requirements that are set out in the regulations.
The requirement to identify hazards, assess and reduce risk is a mandatory requirement set out in Regulation 3.1.; the requirement to have a means of communication in an emergency and a procedure for regular contact as set out in Regulation 3.3. These two regulations will always apply in situations where a person is working alone.
For further information on working alone see WorkSafe WA Guidance Note “Working Alone”.
It is well documented that driver fatigue is the cause of many accidents on our roads, so if your work requires you to drive long distances or travel at odd hours, even minor ailments such as a headache or cold can interfere with your ability to concentrate. Long before you feel drowsy, fatigue has set in. To assist you with managing fatigue, the following should be observed.
-
PLAN YOUR TRIP – PLAN YOUR BREAKS
- Ensure your vehicle is safe: check your oil, water, tyres, brakes and lights. If your carrying or towing a load, ensure it’s stable and secure. Towing a trailer will require extra checks.
- Vehicles or machinery being towed on a trailer should not be permitted to move during transport.
- All vehicles should reduce their speed when travelling on gravel surfaces, vehicles with 4WD should engage 4WD and not exceed 100 km/hr unladen or 80 km/hr when laden or pulling a trailer.
- Avoid driving for more than 8 hours in one day.
- To delay the onset of fatigue the vehicles interior should be well ventilated.
- Complete breaks from driving should be taken every 1 1/2 hrs to 2 hrs depending on demands and conditions.
- When stopped, get out of the car and walk around to exercise the limbs and stimulate the blood circulation.
- Stopping gives you an opportunity to refresh with a drink and do a spot check on the vehicle to ensure everything is safe. Alcohol is to be avoided whilst driving.
- The eye lids feel heavy;
- Day dreaming occurs;
- Traffic situations are misjudged;
- Vehicle speed varies for no apparent reason;
- The vehicle wanders over the road;
- There is a feeling of being cramped and you get the fidgets;
- Continual yawning cannot be prevented.
- A trip should be planned to include a good nights-sleep before travelling.
- If possible a trip should be started early in the day, and not continue late into the night.
- Regular breaks should be taken, get out of the car and exercise.
- When possible, share the driving
ONCE FATIGUE SETS IN – THE ONLY CURE IS SLEEP
- Driver Fatigue information supplied by WA Police – Road Safety Section
Date published: 25/07/2013
Document ID:
|
25
|
Last reviewed:
|
13/03/2009
|
Revision No:
|
15
|
Approved by:
|
..
|
* -25/07/2013 12:27:06 PM